BROOKSを感じる旅、いざイギリスへ
この度、BROOKSのサドルのリペアについて学べるということでイギリスバーミンガムのBROOKS工場まで行ってきた。
久しぶりのイギリス、そしてバーミンガム。
ヒースロー空港についたら、電車に乗ってまずロンドン市内に。
チケット高いし、環状線と思ったらスイッチバックして元の駅に戻ってしまったり結構大変…
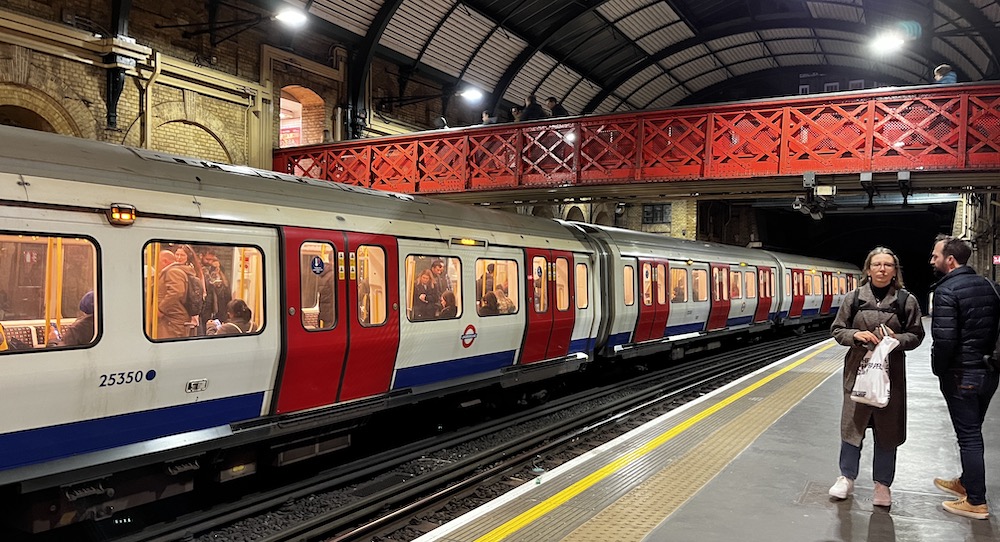
そこからバーミンガムへさらに電車で移動。
特急電車で北へ1時間でバーミンガムへ
翌朝、バーミンガムの工場へ。
過去10年の間に何度か行った事があるけど、いい意味で何も変わらない。
なんといっても150年以上の歴史があるBROOKS。そりゃそんなに簡単に変わらないし、変わらないことに価値があるなと改めて思う。
レザーサドルの最新のモデルはすでに数十年が経過。
作り方も同じ。こんなメーカー他になかなかない。
BROOKSの作り方を一からおさらい(皆様のサドルもお手元にご用意を)
リペアの講習に入る前に、改めてサドルの作り方を一から工場の中を歩きながら紹介してもらった。
細かい点は、改めて次の記事で紹介しようと思うが、数十年変わらないそのサドルの作り方を一から見てみよう。
(BROOKSのレザーサドルをお持ちの方がいたら、ぜひお手元に用意して見て頂くといただくと、その価値がより伝わり、愛着も増すと思います!!)
BROOKSの工場はそれほど大きくはなく、主に2つに大きく分かれている。
主にメタルパーツを生産する場所と、レザーを加工する場所。写真はメタルパーツエリア。
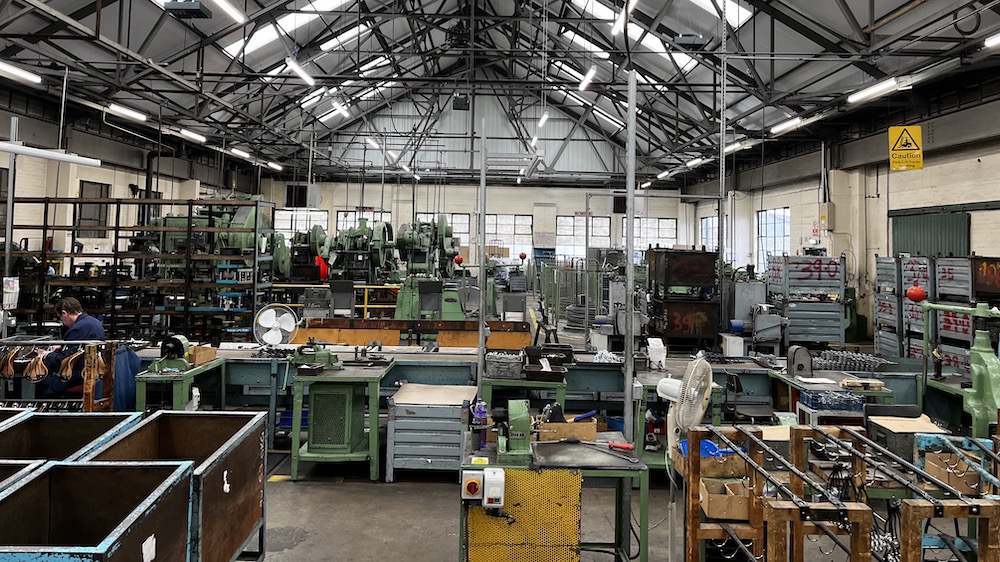
BROOKSの生き証人Steven Green氏
親子2代に渡りBROOKSの工場で働くアイコン的な存在である、スティーブン・グリーンに工場を案内してもらう。
”Steven Green is the Legend”と呼ばれるほど、BROOKSの歴史の多くの部分に親子で関わってきたまさに生ける伝説。
とは、言っても超きさくでフレンドリー。
何でも知ってて、何でも教えてくれる、一度会うと大好きになるキャラクターの方。
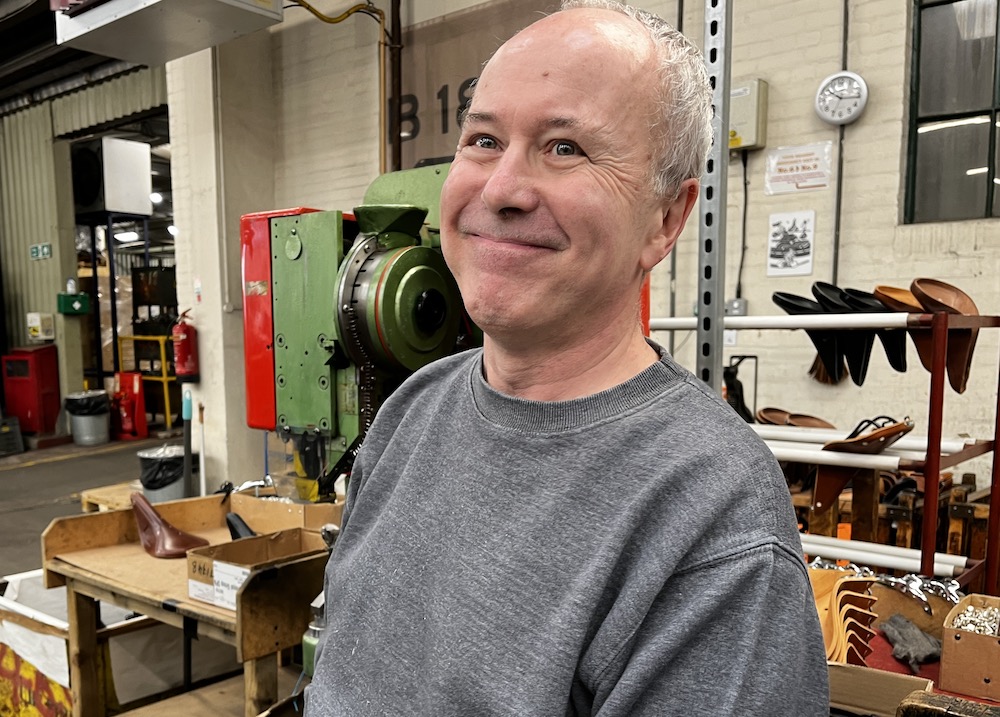
サドルフレームの素材
では、サドルの作り方を見ていこう。
まずメタル工場、の前に素材置場チェック。
この巻かれているのが、レールの元や、フレームの元になる素材たち。
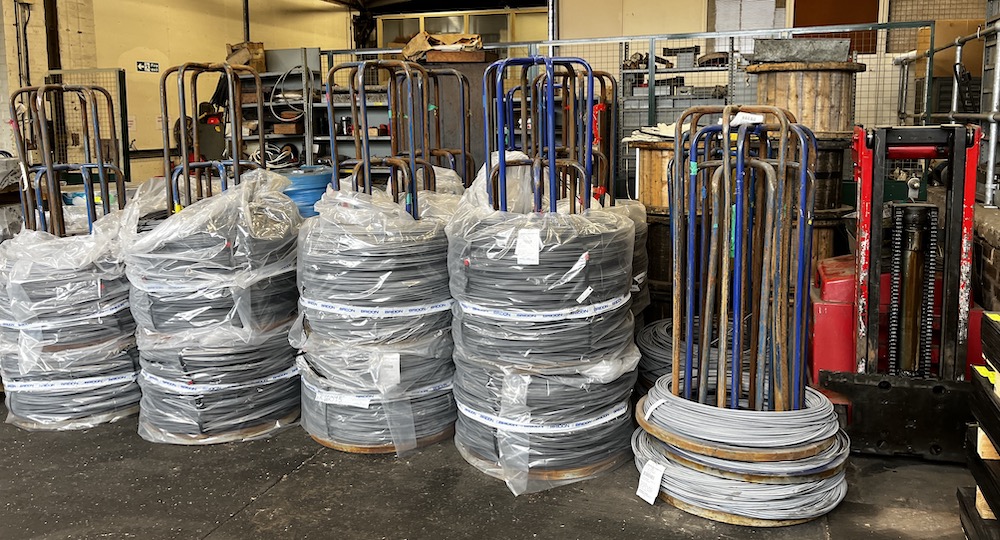
機械もまたビンテージ
レールになる素材、フレームになる素材を、これまたビンテージの機械に通して加工を行う。
一番古い機械だと、70-80年くらい経っているとのこと。
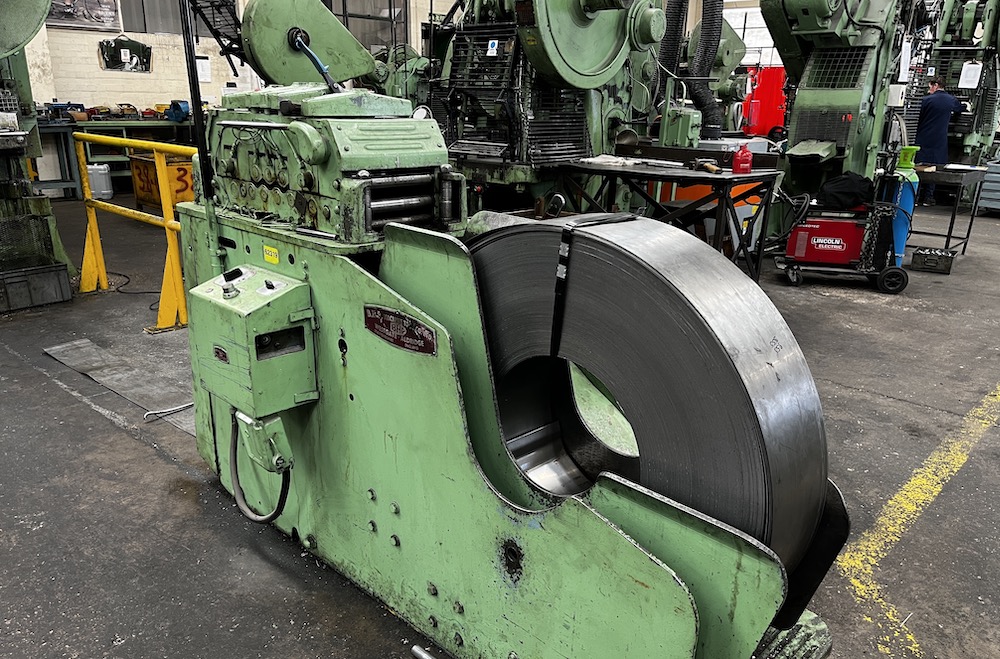
バネ一つにもストーリーが
バネを作る機械は、右用、左用と2種類存在する。
この機械を作動させるとバネがカットされて次々に生まれてくる。

約50年前(もっと前かも)までは、両方同じ巻き方のバネを使用していたそう。
そうすると、厳密にいうと、サドルの沈み方に癖がついて片側に寄る癖がついてしまうため、左右別の巻き方をし始めたというストーリーが。
ライトハンド、レフトハンド
わかりやすく、右用は、RH(ライトハンド)、左用はLH(レフトハンド)の字が書いてある。
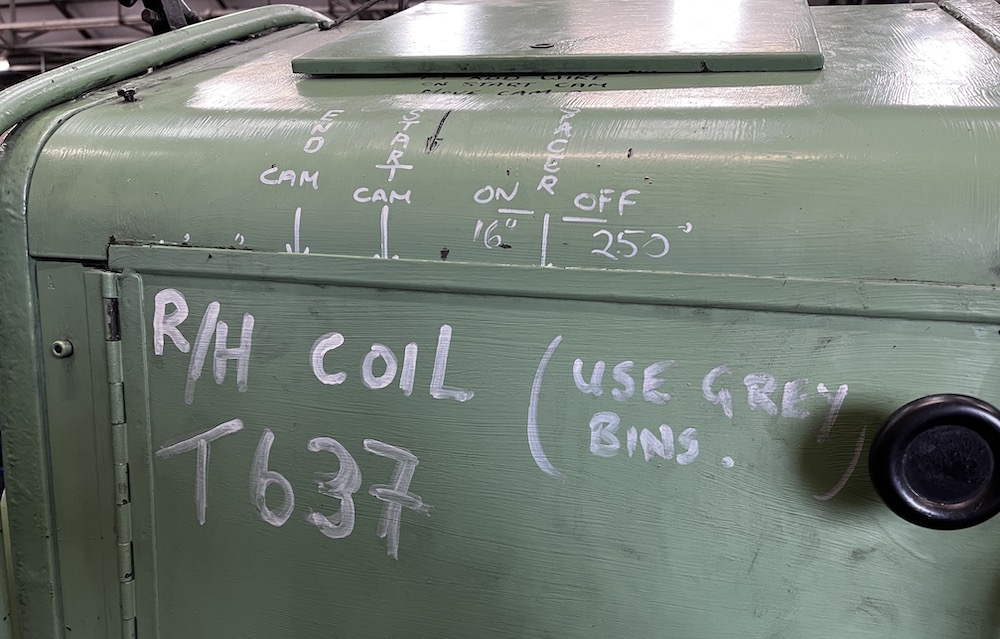
B33のツイストしたバネを作る機械は、数年前よく壊れていたが、ついに修理を諦めて、外注部品になったとのこと。
機械まで希少に。
1本の棒がサドルレールの形に
レールはこの細い鉄の棒を機械に通して曲げてカット。
各モデルの見本たち。
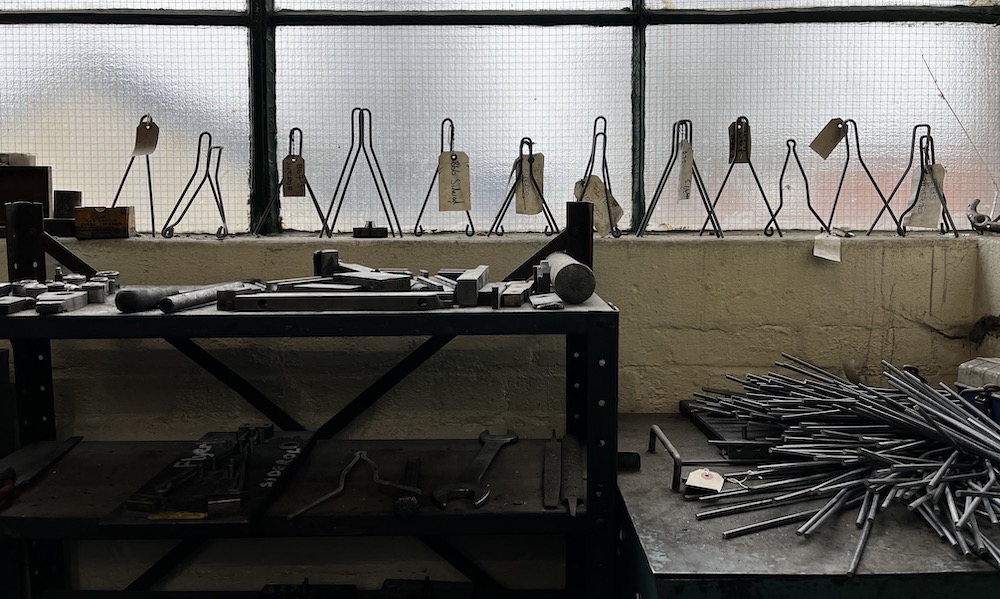
さらに、立体的に曲げていくと見慣れた形に。
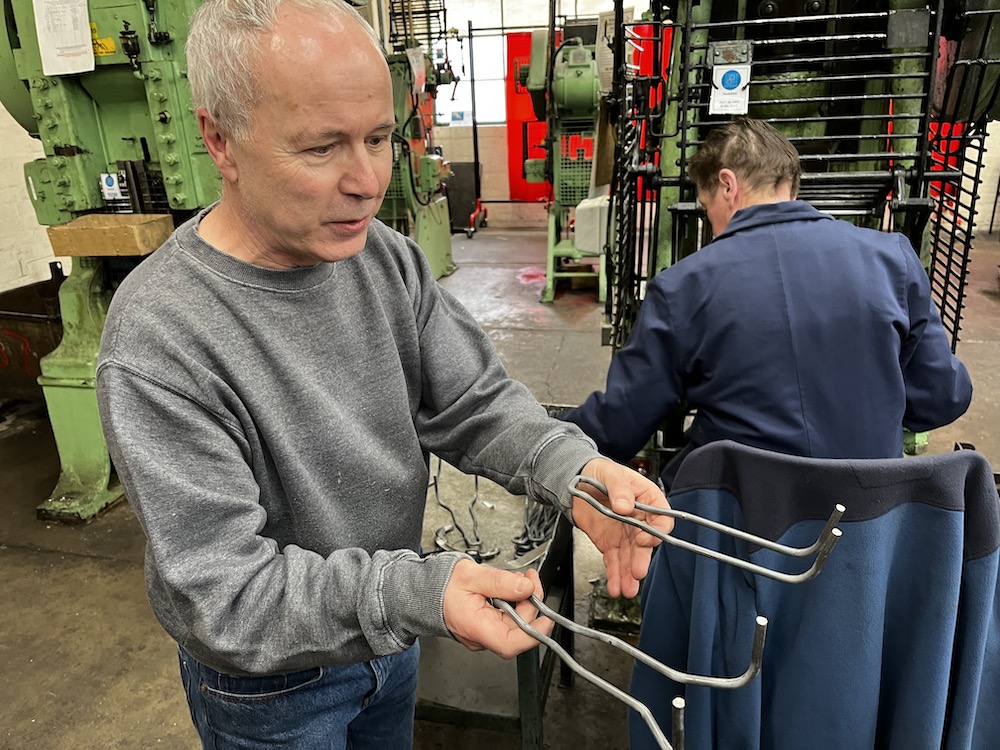
フレームの完成
レールを、プレスしたバックプレートと溶接して、フレームが出来上がる。
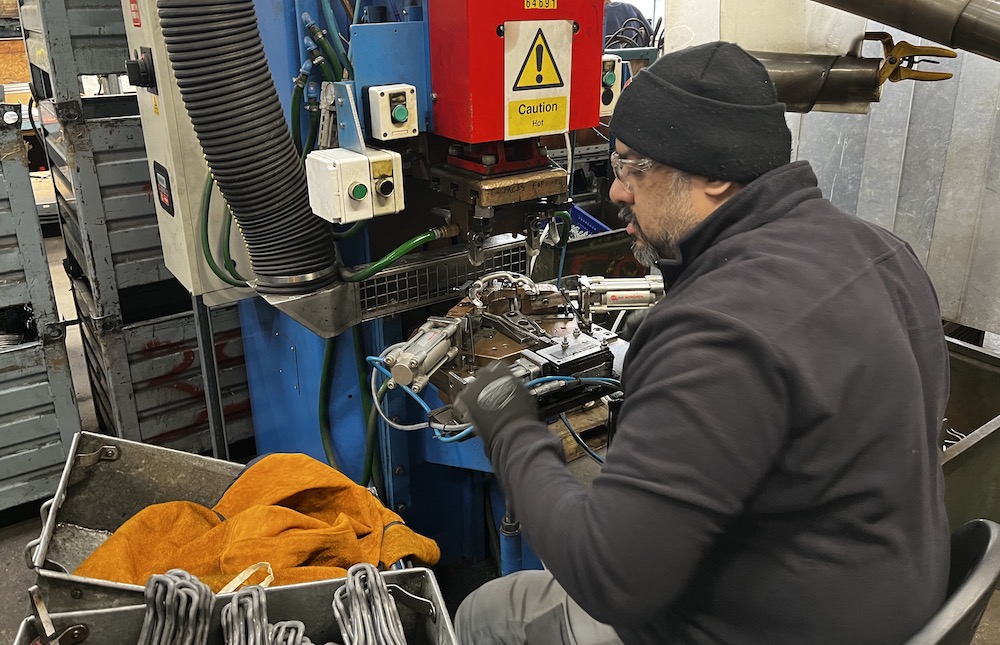
もう少し手のこんだフレーム
B17のようなものであれば、ここでフレームは完成。
B33、B190などのヘビーデューティーなサドルはさらにフレームを重ねてボルト留する工程がある。
バネを組み付けていく作業。ヘビーデューティーなやつは、
たくさんパーツがある上に、ただ組み付ければ良いだけでなく、ハンマーでガンガン叩きながら形も整えていく。
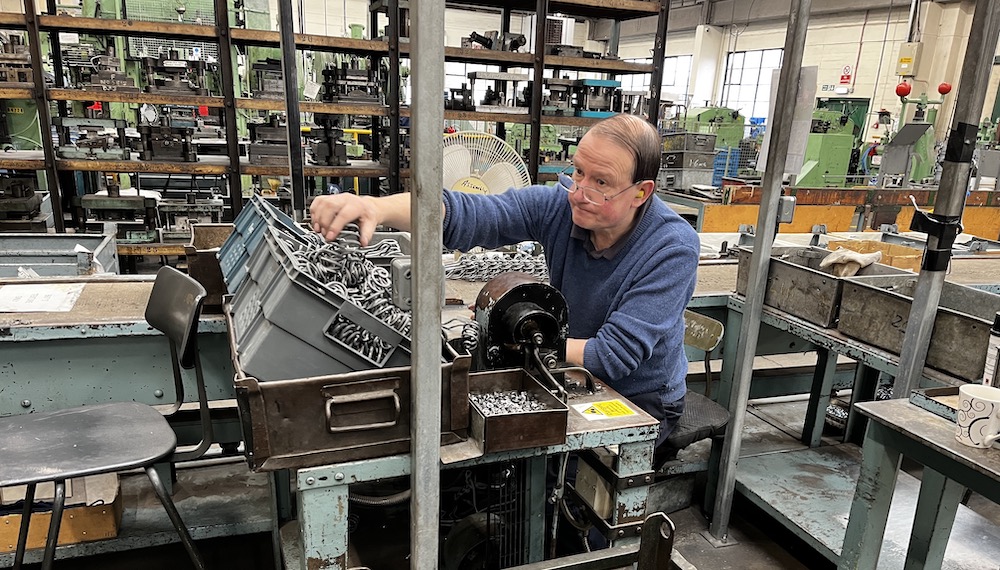
このおばちゃんの組付けから、さらにテンションピンのためのネジタップまで切る一連の流れがかっこよかった。
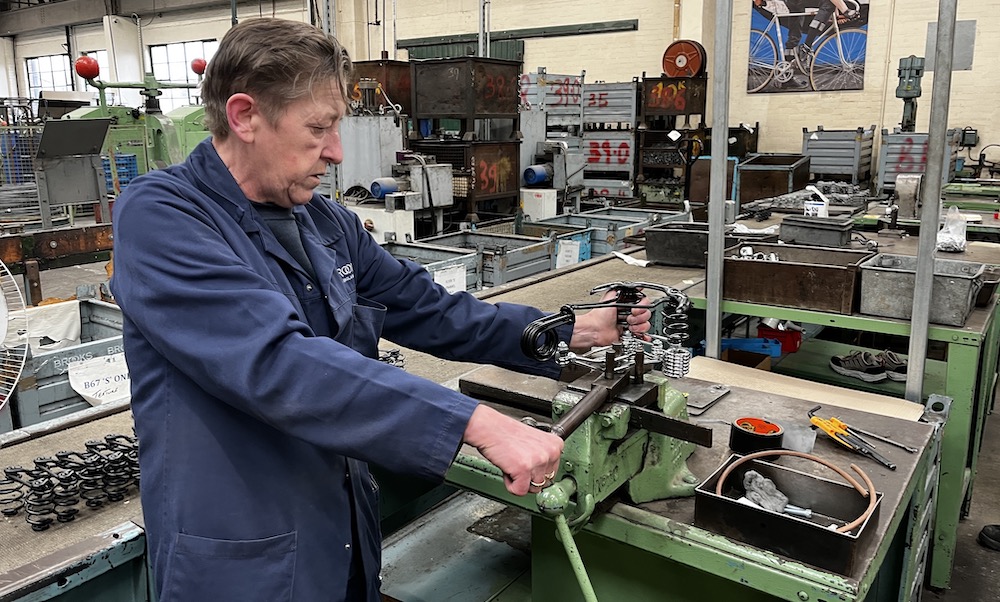
こうやってヘビーデューティーモデルの、複雑なフレームが仕上がる。
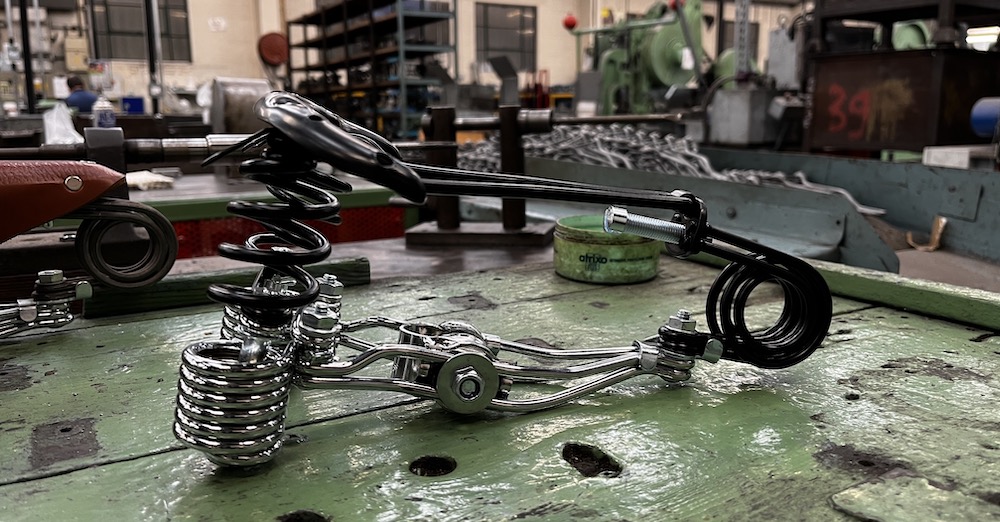
レザートップの作り方
次にレザー工場側に。
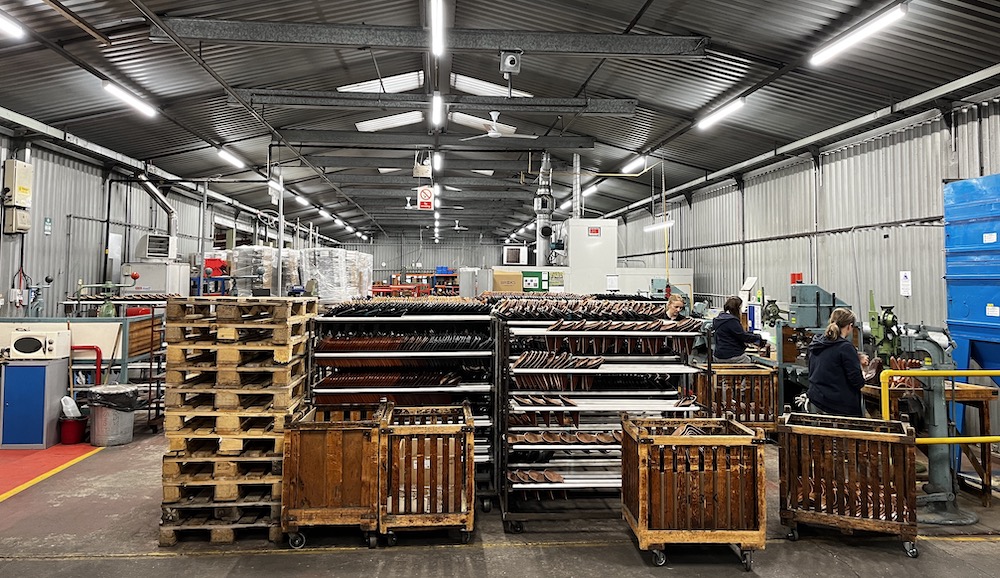
レザーももちろんプレミアム
この平べったい革のシート。
牛舎でなく、のびのびと放牧された牛の革は傷も少なく、北欧のタンナーに送られ仕上げられイギリスに帰ってくる。
スペシャルなレザーのため、その入手の可否は長年に渡る関係性による部分も大きい。
新規参入が難しく、BROOKSの独立性が保たれている。
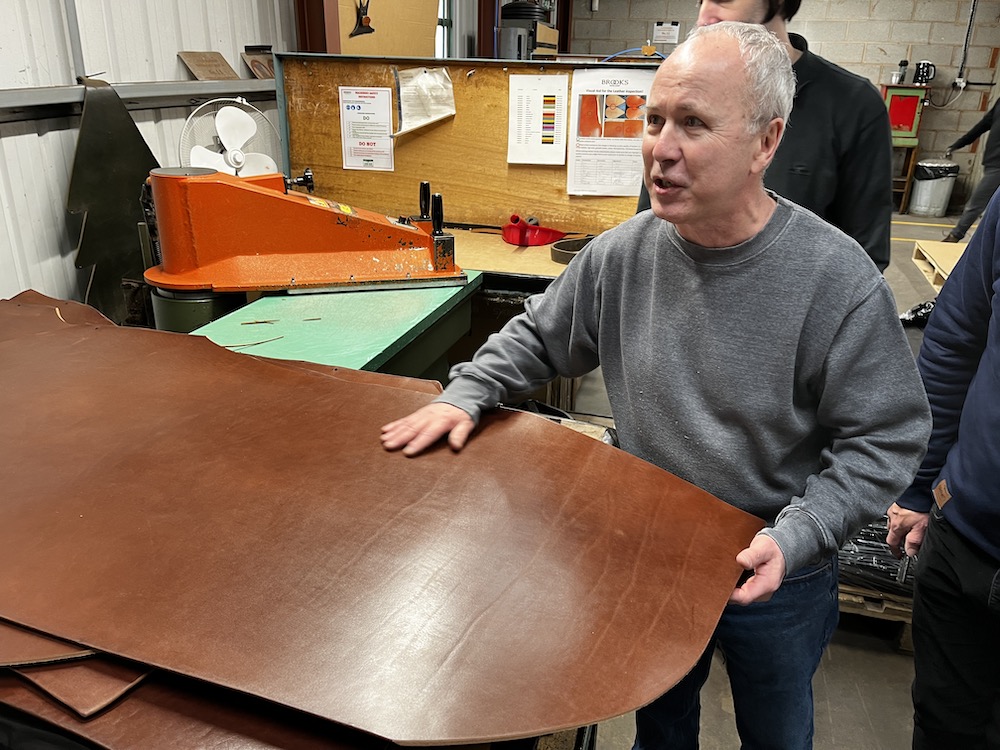
背中の部分を使用、本革の個性
サドルに適したレザーは背中の部分。
腹は柔らかすぎ、肩は薄すぎるため、背中がベストだそう。
レザーのシートを見てみると様々な柄が浮かび上がっている。
血管の跡(血筋)が模様で走っている。
この筋は嫌がられてしまうこともあるが、これこそ本革の証で、この模様があるとより個性が出てきて自分だけのサドル感が出てくるのでぜひ楽しんで頂きたいポイントの一つ。
シートからサドルサイズにカット
これを伸びる方向など繊維の向きを見ながら、サドルに適した方向で、型で抜き取っていく。
同時に、B17のアイコン的な3つの穴も空いているのがわかる。
抜ききれなかった部分はグリップなどに再利用される。
さらに余った革で、後ろに写っているバットマン?だったり、クリスマスツリー型だったりシーズンによっておもしろカットが見られる。
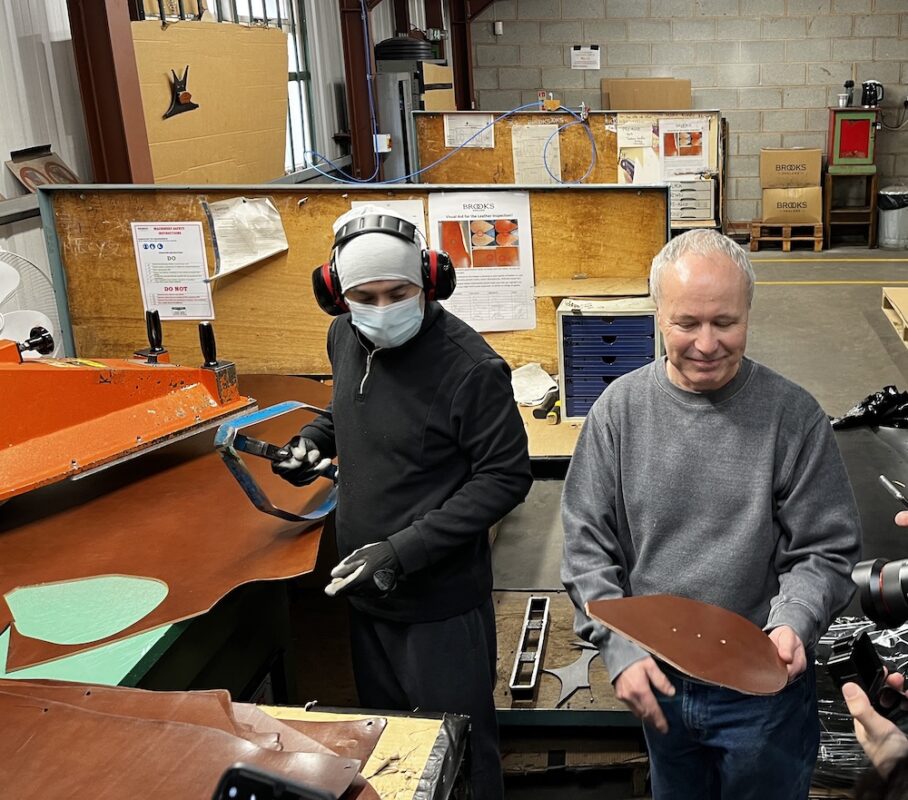
レザーを水に浸す
この型抜きされたレザーは、プールで水に浸される。
革を水分で柔らかくして、次の成型の工程に進む準備。
サドルを水に濡らすのがあまりよくないのは、この工程のように成型をしやすいコンディションにしてしまうので、型崩れにつながるということ。
BLACK、BROWN、HONEYでそれぞれプールが分かれている。
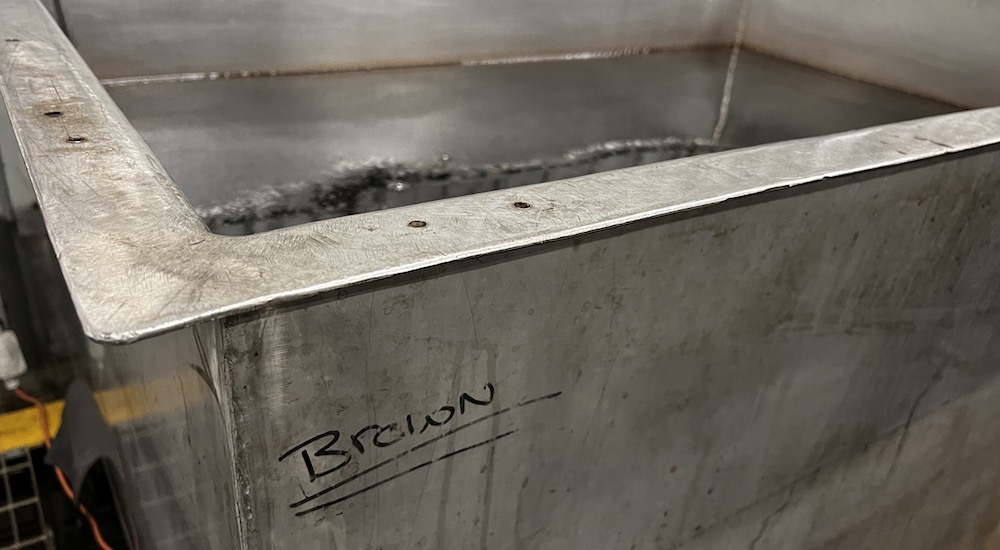
何かやばそうな、特殊な液体に見えるが、単に水。
多分同じような質問が多いせいか、スティーブングリーンが、これは酸で、手をいれたら…ウワーーー!!とお茶目なジョークを挟んでくる。
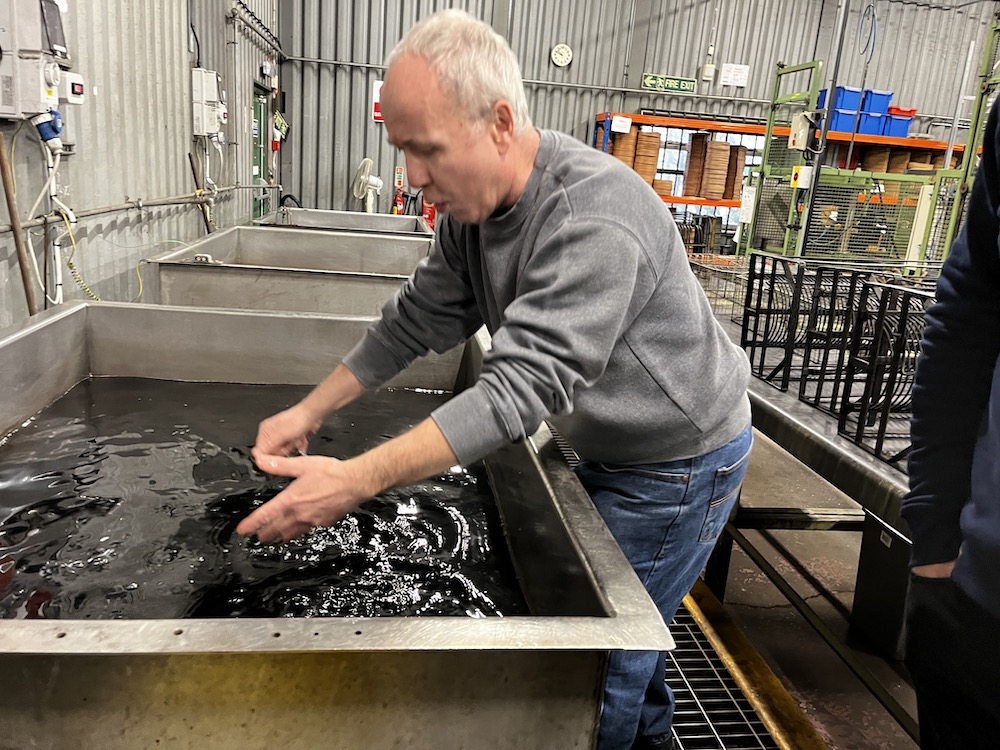
成型待ちのレザートップの元がスタッキングされている。
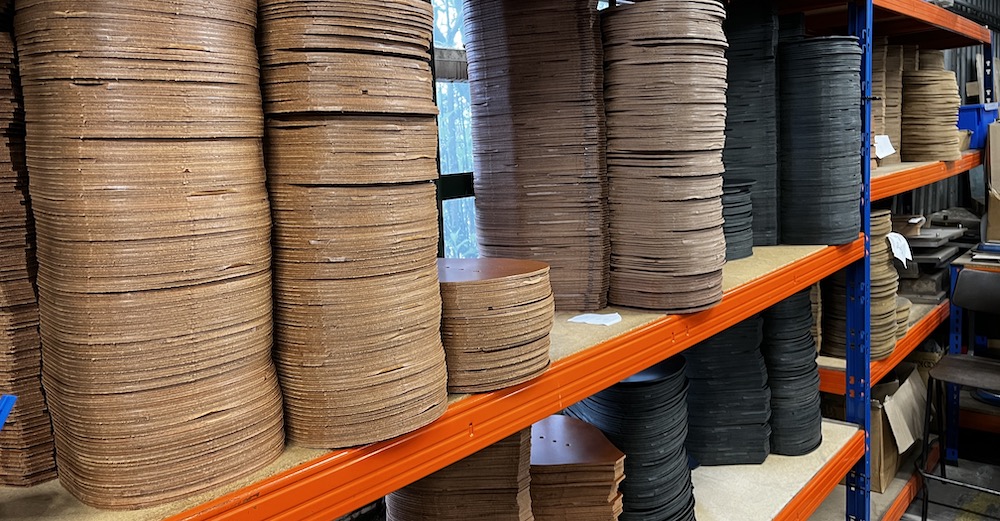
プレスして成型&余分なレザーをカット
これをサドルの型でプレスし、成型、余分な革をカット。
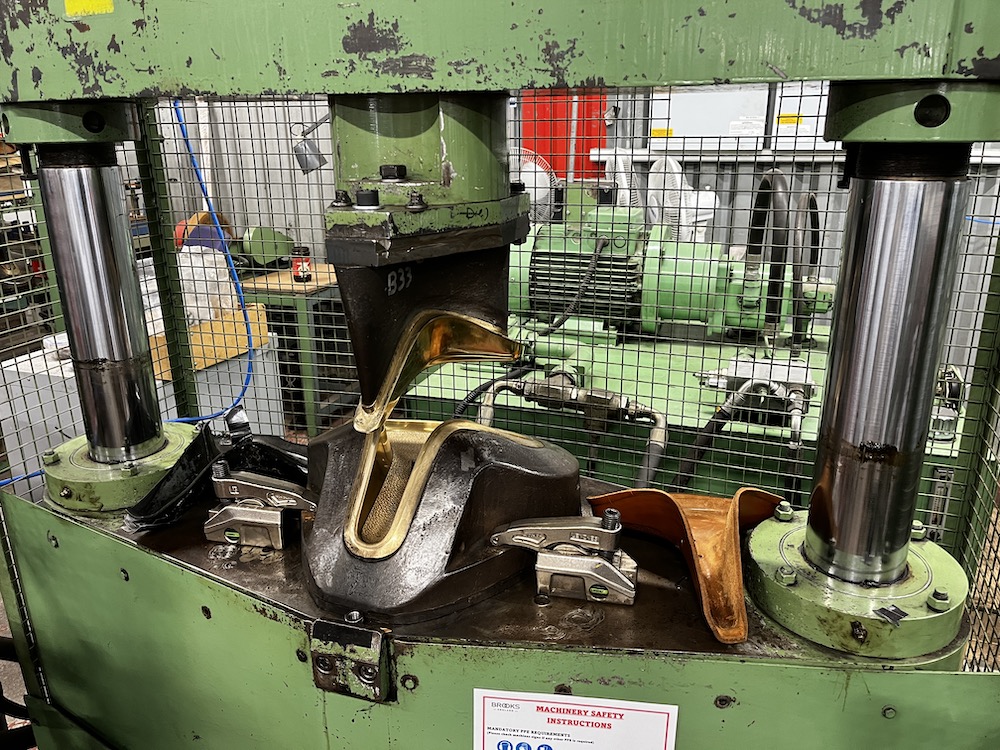
歴代の型たちが保管されていて、製造年月日が刻印されているが、すでに数十年使い続けられていることがわかる。
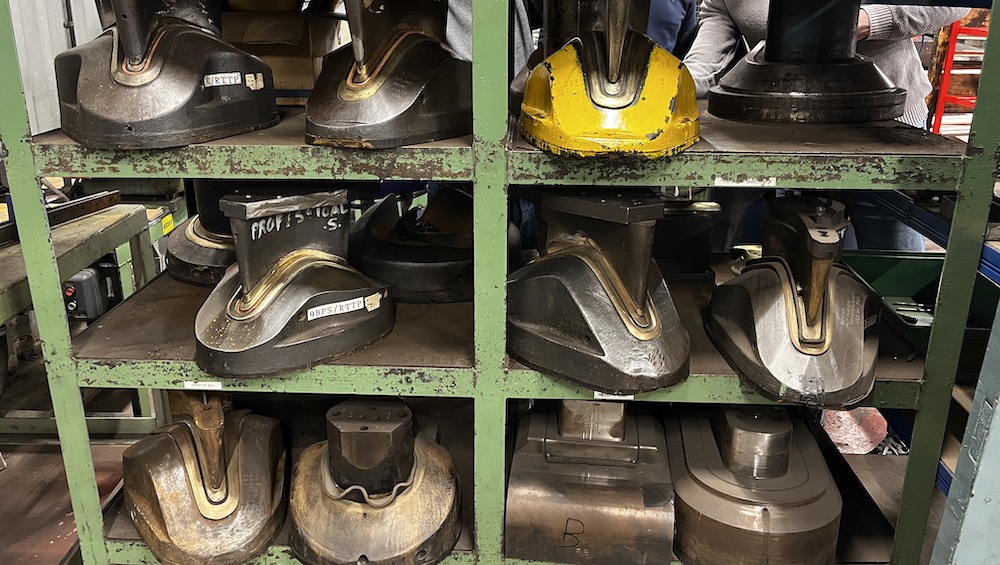
残った水分を抜く
その後窯で、90分乾燥させる。
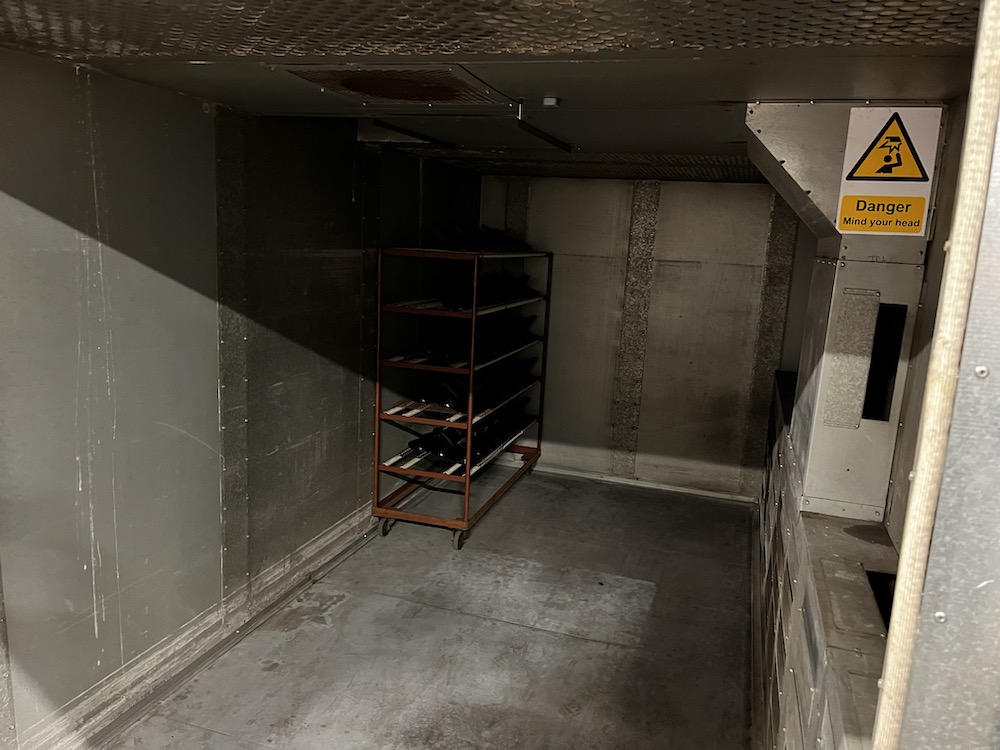
サドルトップの仕上げ工程に
その後エッジのザラザラをヤスリできれいに。
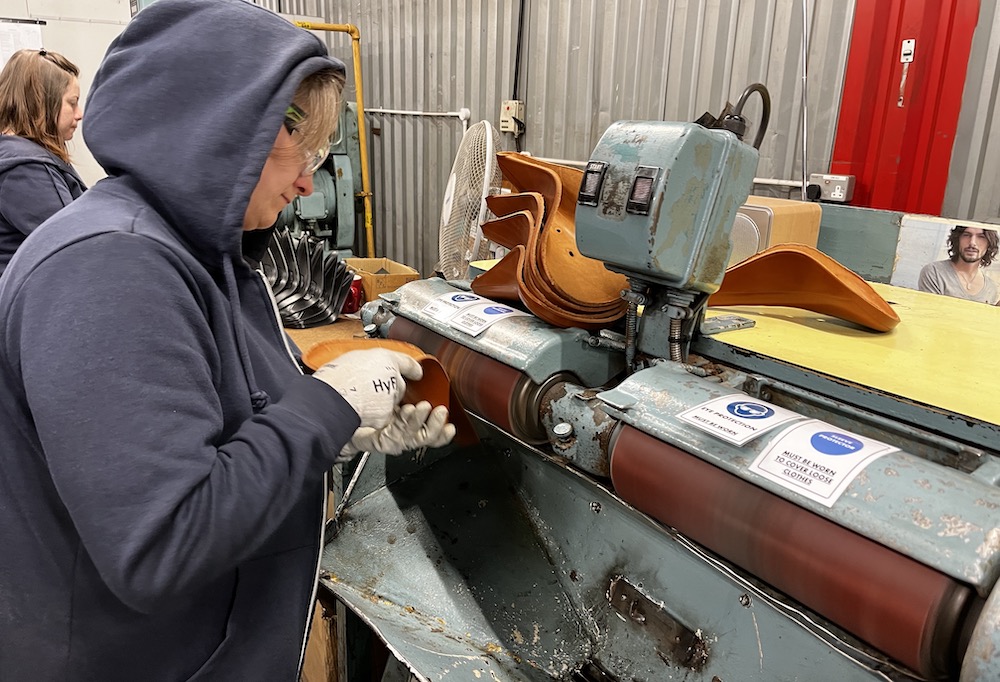
左が加工前、右が加工後
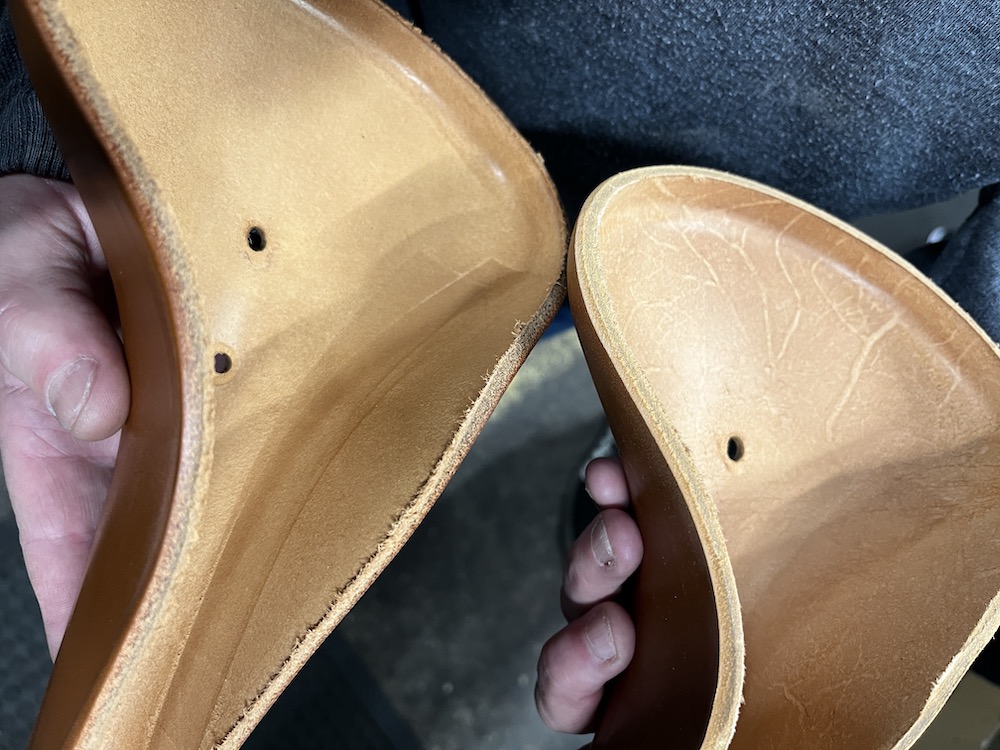
この後、サドルトップに、モデルのエンボスのプレス。
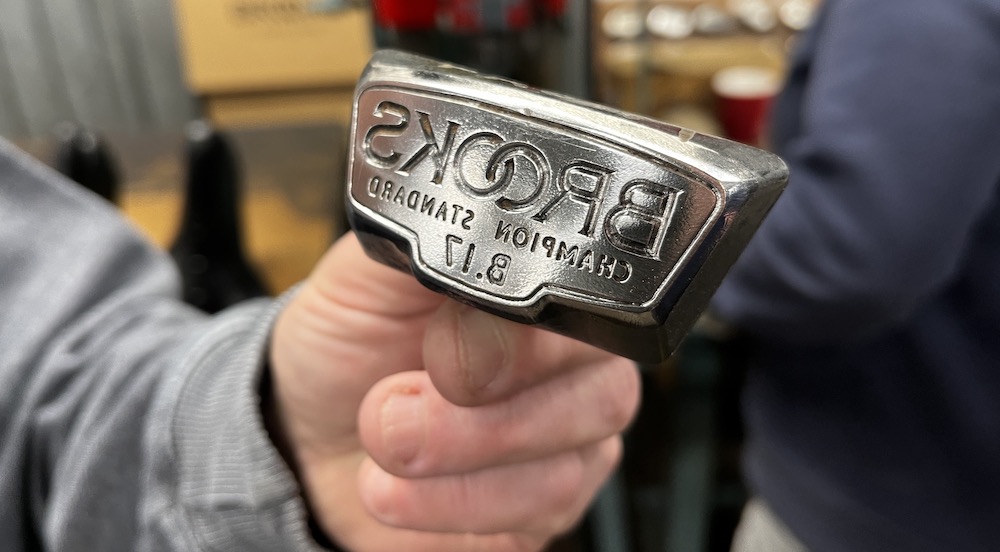
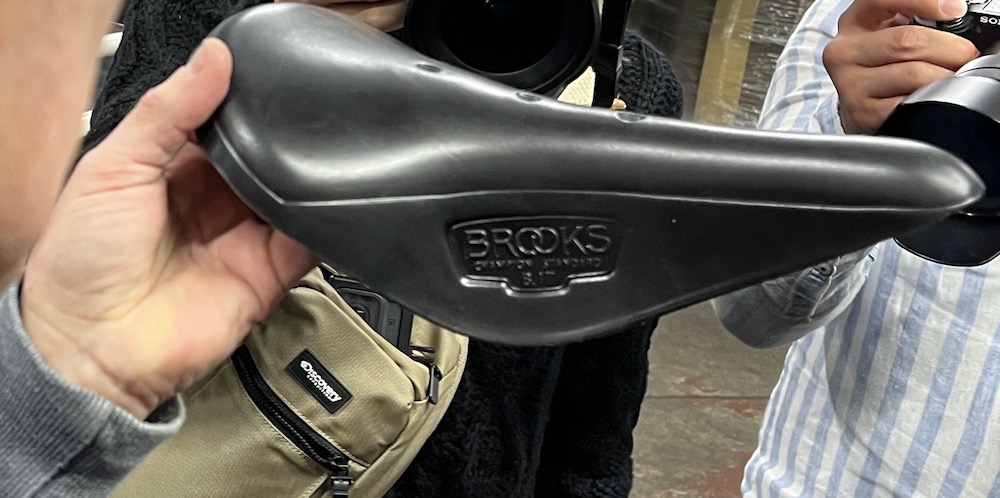
プレスの時についたセンターのポイントに合わせて
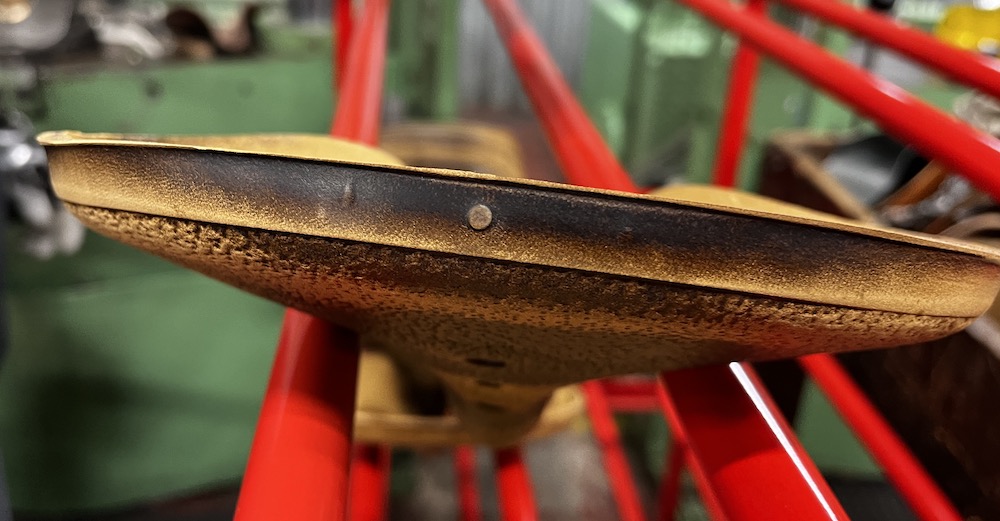
プレートを取り付ける。
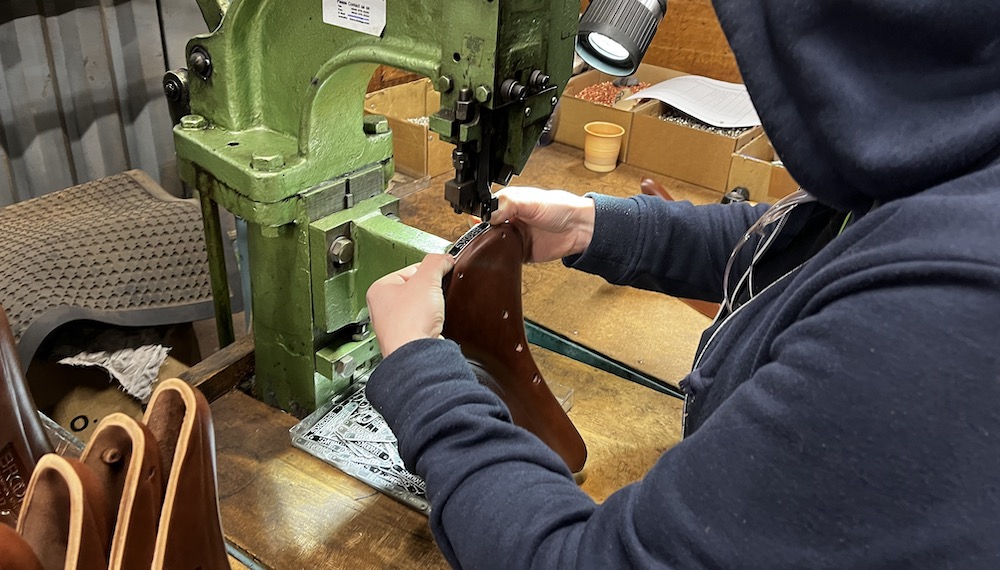
こうしてサドルトップが完成。
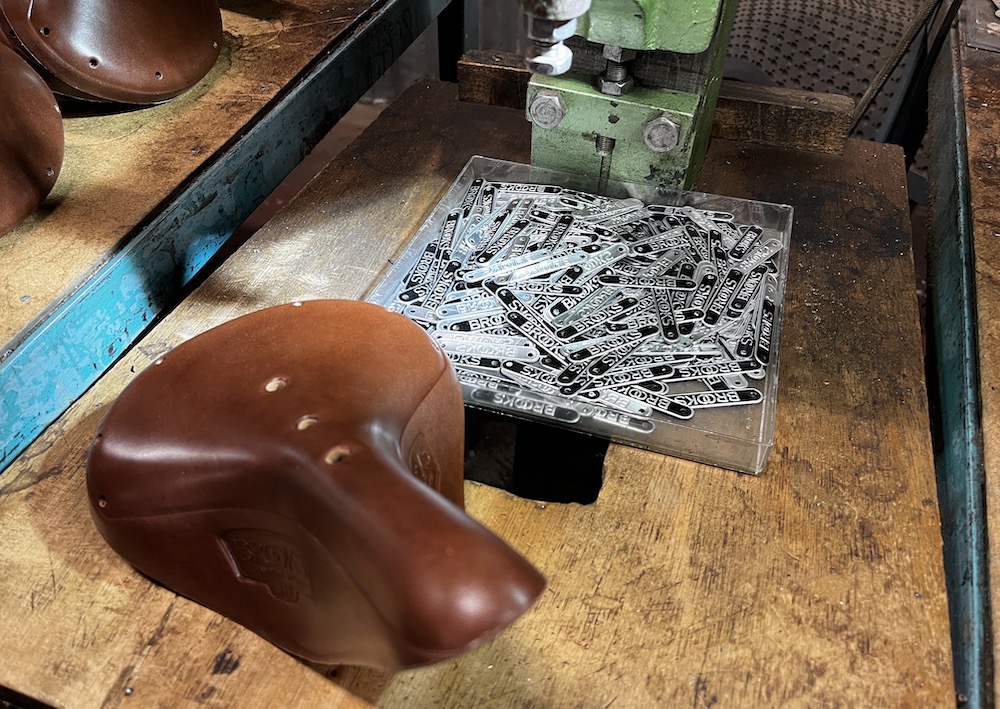
サドルトップとフレームを一つにして完成に向かう
そして今、フレームと、トップが仕上がった。
これを一つにする工程。
ここで大きく分かれる。
スタンダードサドルは、スチールリベットで仕上げて完成
STANDARDと呼ばれる、スチールリベットの加工では、ここから機械でスチールリベットを打ってフレームとくっつけていく。
リズムよく、前3箇所、後ろ6箇所を仕上げたら完成。
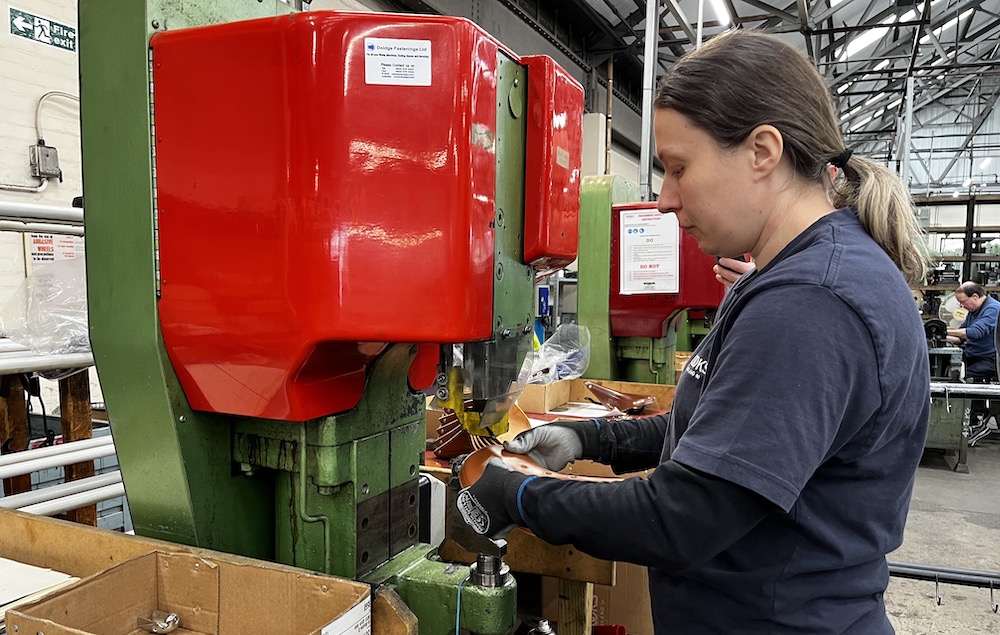
スペシャルサドルはここからが長い
SPECIALと呼ばれる仕上げは、ここからさらに職人たちの一つ一つ手作業によりスペシャルな仕上げが施される。
スペシャルな技の詳細は改めてご紹介。
ざっくり言うと、銅鋲を打つ仕上げ。
ザグリ加工
銅鋲が収まるためのザグリを入れる機械がフロント用、リア用で2種。
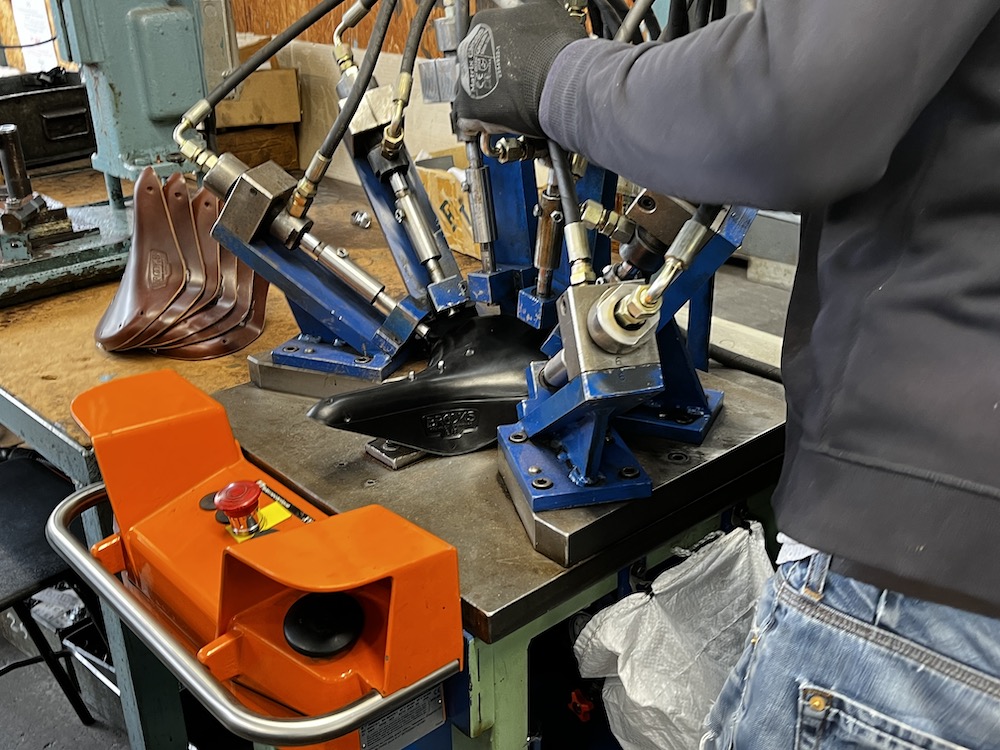
サイドカット
サイドの足が当たる部分をナイフでカットしていく。
これが実は一番むずかしいそう。
左右ガイドがあるわけでもなく、職人が目で見て仕上げる。
あまりによく切れるナイフなので、危なくて触らせてもらえなかった。
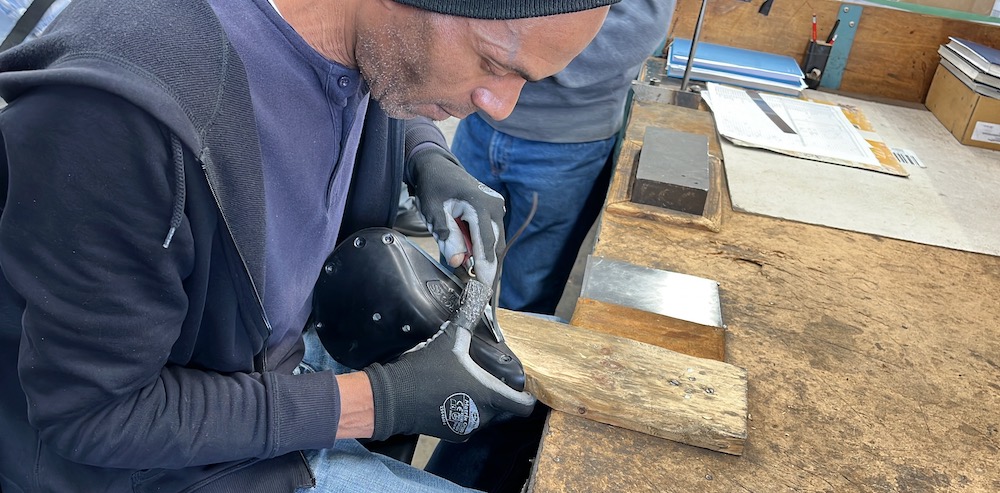
ハンマー仕上げ
そしてお待ちかね?のハンマータイム!
ハンマーは2種。この長細いハンマーはリベットのとんがっている方を潰すためのもの、
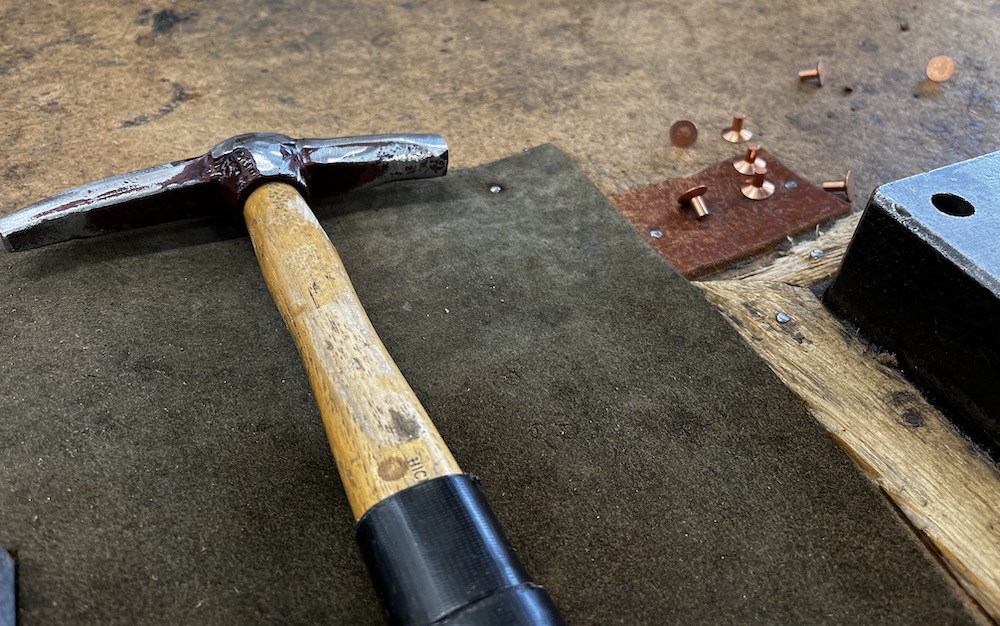
リベットの先端を潰すハンマー
まず前3つのフロントパーツをレザーにセットして、レザーのざぐり部分に鋲を収めて逆から先端をつぶす。
先端をつぶす…これがおそろしく難しい。曲がった細いハンマーで、鋲の先っぽを潰すのだが
こんな感じ。いや無理!と思う瞬間。
一応、この作業用の機械もあるけど、それもまたなかなか難しい。
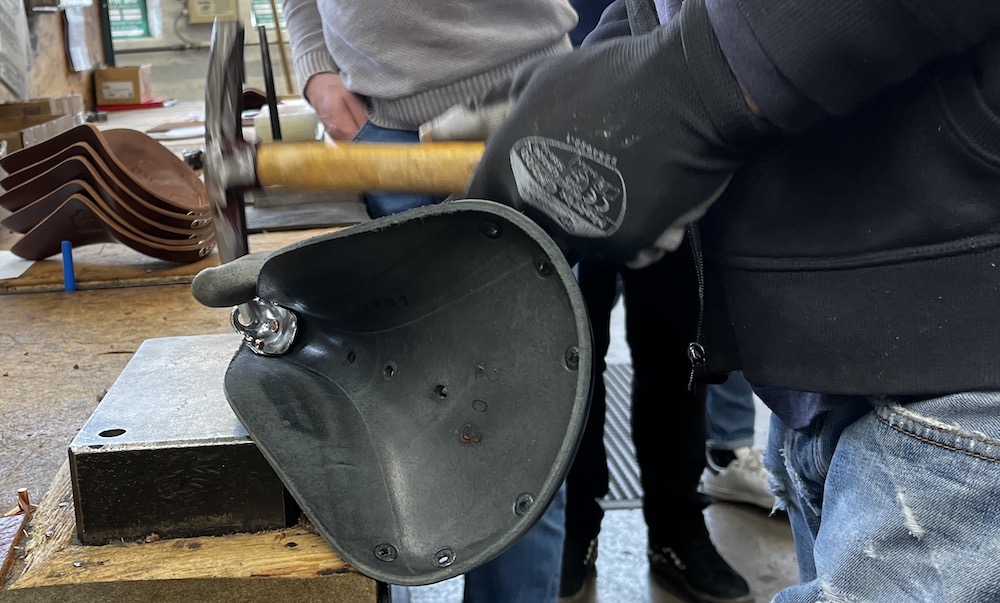
表からハンマーで仕上げ
前側3つ、後ろ側6つの鋲の先をつぶしたら、今度は表からハンマーで叩いて仕上げる。
さっき潰した裏側を治具に当てて、表から2回鋲の中心を叩き、あとは周囲を叩いてなじませていくx9箇所。
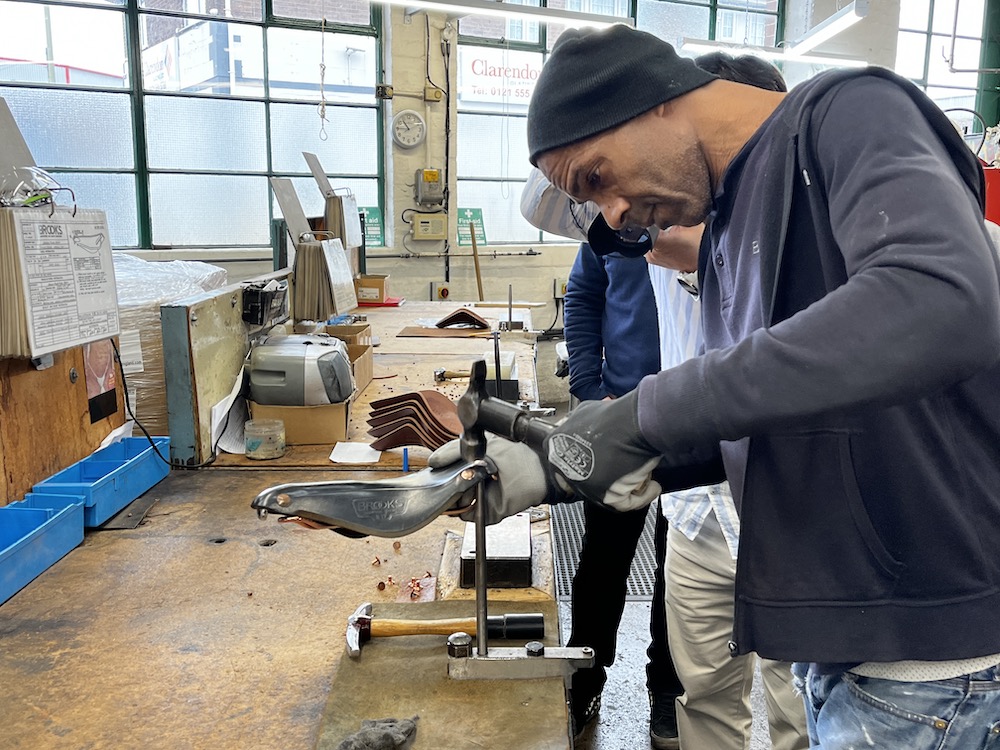
職人が叩いてきれいに仕上がるとこんな感じ。
中心2回、後は周囲を叩いてなじませる。美しい…
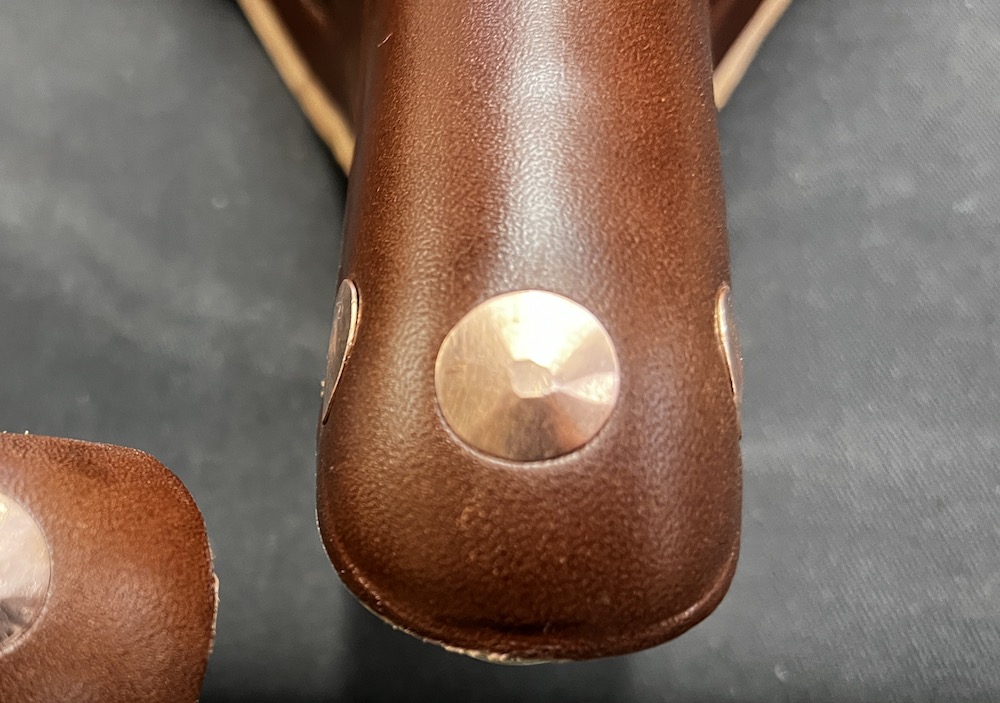
1:25の価値
スペシャルサドルが1個できる時間で、スタンダードサドルは25個生産されるそう。
価格の差としては5000円にも満たない差だが、こんなにも多く手がかかっている。
BROOKSは存在そのものがスペシャル
製品になると一つのサドルだけど、たくさんの人の手を経てそのサドルが仕上がっている。
この写真に写っている誰かの手を通って今手元にあるサドルがあると思うと感慨深い気持ちになる。
工場も機械もビンテージ、希少なレザー、そして数少ない職人、今こうしてまだ変わらぬ製法でレザーサドルが手に入ること自体が本当にすごい事だと思う。
次回は、リペア講習で体感したスペシャルサドルのクラフトマンシップについてもう少し掘り下げていきます!